Слайд 2
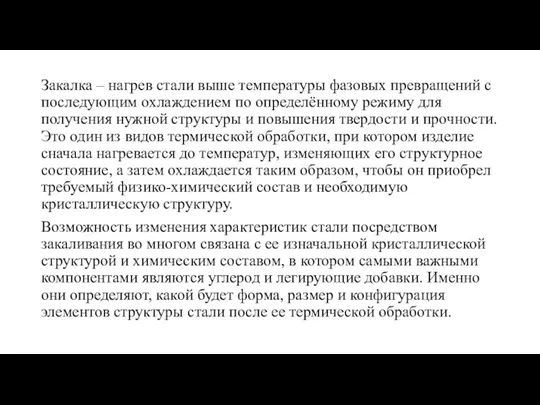
Закалка – нагрев стали выше температуры фазовых превращений с последующим охлаждением
по определённому режиму для получения нужной структуры и повышения твердости и прочности. Это один из видов термической обработки, при котором изделие сначала нагревается до температур, изменяющих его структурное состояние, а затем охлаждается таким образом, чтобы он приобрел требуемый физико-химический состав и необходимую кристаллическую структуру.
Возможность изменения характеристик стали посредством закаливания во многом связана с ее изначальной кристаллической структурой и химическим составом, в котором самыми важными компонентами являются углерод и легирующие добавки. Именно они определяют, какой будет форма, размер и конфигурация элементов структуры стали после ее термической обработки.
Слайд 3
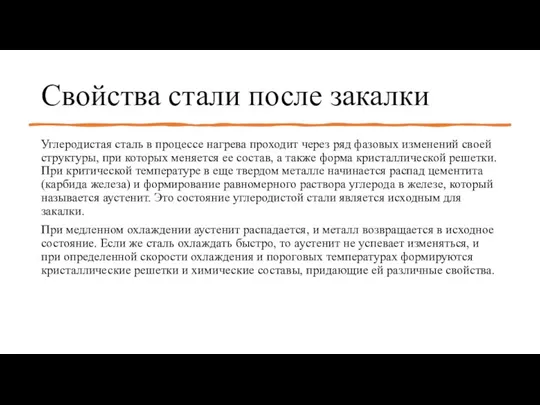
Свойства стали после закалки
Углеродистая сталь в процессе нагрева проходит через ряд
фазовых изменений своей структуры, при которых меняется ее состав, а также форма кристаллической решетки. При критической температуре в еще твердом металле начинается распад цементита (карбида железа) и формирование равномерного раствора углерода в железе, который называется аустенит. Это состояние углеродистой стали является исходным для закалки.
При медленном охлаждении аустенит распадается, и металл возвращается в исходное состояние. Если же сталь охлаждать быстро, то аустенит не успевает изменяться, и при определенной скорости охлаждения и пороговых температурах формируются кристаллические решетки и химические составы, придающие ей различные свойства.
Слайд 4
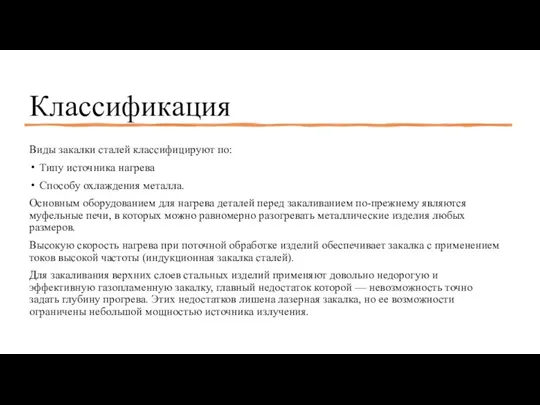
Классификация
Виды закалки сталей классифицируют по:
Типу источника нагрева
Способу охлаждения металла.
Основным оборудованием
для нагрева деталей перед закаливанием по-прежнему являются муфельные печи, в которых можно равномерно разогревать металлические изделия любых размеров.
Высокую скорость нагрева при поточной обработке изделий обеспечивает закалка с применением токов высокой частоты (индукционная закалка сталей).
Для закаливания верхних слоев стальных изделий применяют довольно недорогую и эффективную газопламенную закалку, главный недостаток которой — невозможность точно задать глубину прогрева. Этих недостатков лишена лазерная закалка, но ее возможности ограничены небольшой мощностью источника излучения.
Слайд 5
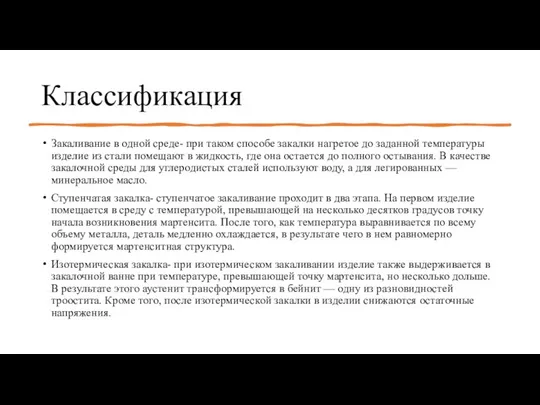
Классификация
Закаливание в одной среде- при таком способе закалки нагретое до заданной
температуры изделие из стали помещают в жидкость, где она остается до полного остывания. В качестве закалочной среды для углеродистых сталей используют воду, а для легированных — минеральное масло.
Ступенчатая закалка- ступенчатое закаливание проходит в два этапа. На первом изделие помещается в среду с температурой, превышающей на несколько десятков градусов точку начала возникновения мартенсита. После того, как температура выравнивается по всему объему металла, деталь медленно охлаждается, в результате чего в нем равномерно формируется мартенситная структура.
Изотермическая закалка- при изотермическом закаливании изделие также выдерживается в закалочной ванне при температуре, превышающей точку мартенсита, но несколько дольше. В результате этого аустенит трансформируется в бейнит — одну из разновидностей троостита. Кроме того, после изотермической закалки в изделии снижаются остаточные напряжения.
Слайд 6
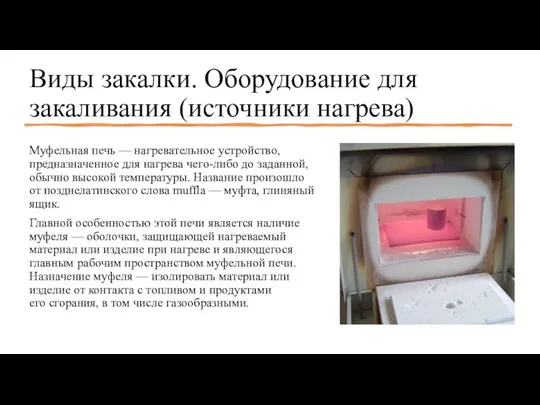
Виды закалки. Оборудование для закаливания (источники нагрева)
Муфельная печь — нагревательное устройство, предназначенное
для нагрева чего-либо до заданной, обычно высокой температуры. Название произошло от позднелатинского слова muffla — муфта, глиняный ящик.
Главной особенностью этой печи является наличие муфеля — оболочки, защищающей нагреваемый материал или изделие при нагреве и являющегося главным рабочим пространством муфельной печи. Назначение муфеля — изолировать материал или изделие от контакта с топливом и продуктами его сгорания, в том числе газообразными.
Слайд 7
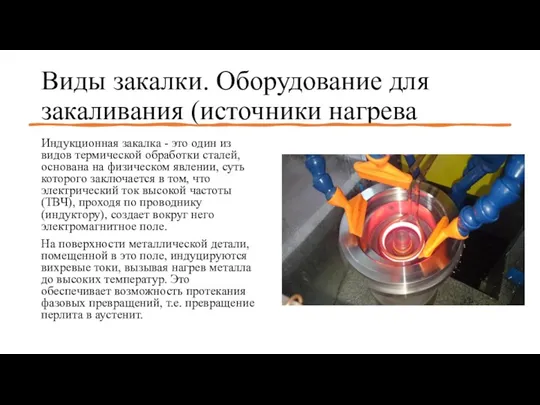
Виды закалки. Оборудование для закаливания (источники нагрева
Индукционная закалка - это один из
видов термической обработки сталей, основана на физическом явлении, суть которого заключается в том, что электрический ток высокой частоты (ТВЧ), проходя по проводнику (индуктору), создает вокруг него электромагнитное поле.
На поверхности металлической детали, помещенной в это поле, индуцируются вихревые токи, вызывая нагрев металла до высоких температур. Это обеспечивает возможность протекания фазовых превращений, т.е. превращение перлита в аустенит.
Слайд 8
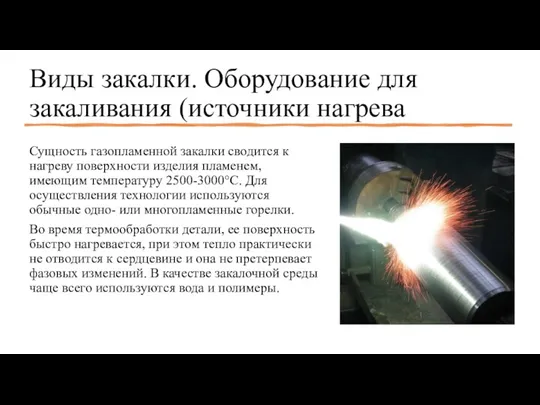
Виды закалки. Оборудование для закаливания (источники нагрева
Сущность газопламенной закалки сводится к
нагреву поверхности изделия пламенем, имеющим температуру 2500-3000°C. Для осуществления технологии используются обычные одно- или многопламенные горелки.
Во время термообработки детали, ее поверхность быстро нагревается, при этом тепло практически не отводится к сердцевине и она не претерпевает фазовых изменений. В качестве закалочной среды чаще всего используются вода и полимеры.
Слайд 9

Виды закалки. Оборудование для закаливания (источники нагрева
Лазерная закалка металлов и сплавов лазерным излучением основано на
локальном нагреве участка поверхности под воздействием излучения и последующем охлаждении этого поверхностного участка со сверхкритической скоростью в результате теплоотвода теплоты во внутренние слои металла.
Слайд 10
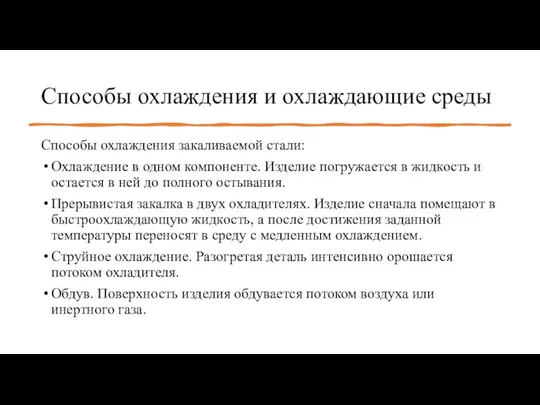
Способы охлаждения и охлаждающие среды
Способы охлаждения закаливаемой стали:
Охлаждение в одном компоненте.
Изделие погружается в жидкость и остается в ней до полного остывания.
Прерывистая закалка в двух охладителях. Изделие сначала помещают в быстроохлаждающую жидкость, а после достижения заданной температуры переносят в среду с медленным охлаждением.
Струйное охлаждение. Разогретая деталь интенсивно орошается потоком охладителя.
Обдув. Поверхность изделия обдувается потоком воздуха или инертного газа.